Case Study: Leaks From Gas Purging Solved For Dairy Processor
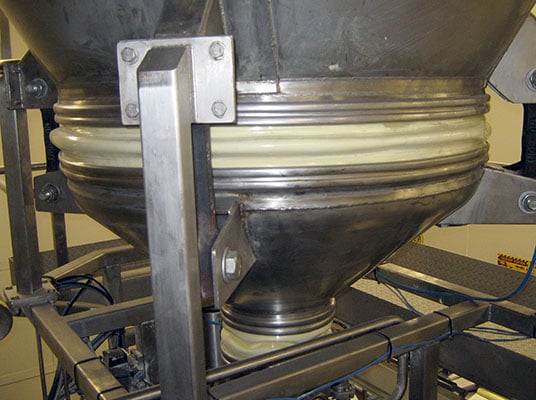
Dairy Better Hygiene Achieved Under Pressure
A leading New Zealand dairy plant had a major challenge with hygiene in their blending filler room.
A vibratory discharging cone was connected to the hopper via a traditional connecting sock and steel clamps. Regular gas purging of the system caused excessive dust leakage and product build-up in the joins – a major hygiene issue.
Since installing the BFM® fitting system, the room is clean and there has been a significant reduction in both downtime and replacement costs.
The Challenge
The regular gas purging of the system forced powder through small gaps in the old-style sock and steel clamp connector.
This caused an unhygienic environment and hours of downtime for regular cleaning. There was also a major contamination point created by significant product build-up between the externally fitted sock and hopper.
It was highly time-consuming to remove and re-fit the steel strapping clamps during sock cleaning & replacement.
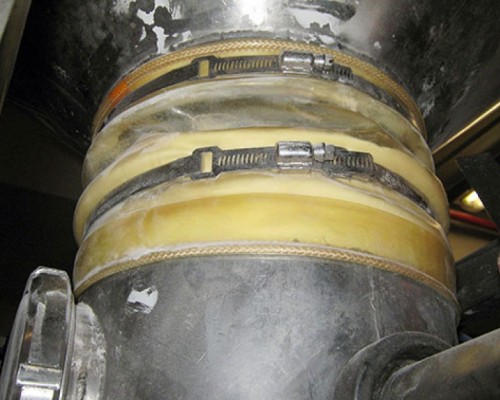
The BFM® Solution
The installation of a BFM® fitting for both the upper and lower connections has created a sealed system, and the filling room is now a dust-free environment.
The pressure from the gas purging no longer causes product leakage, and because the fitting sits inside the spigot, there is no product build-up at the connector joins.
When the fittings do need replacing, it’s now a quick and easy snap-fit process.
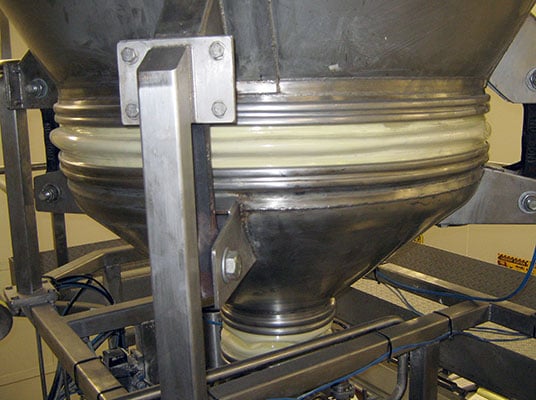
Benefits Achieved
Improved Hygiene
There is no more dust leakage, eliminating cross-contamination of products and reducing general housekeeping costs.
Quick Changeovers
The quick and easy snap-fit of our BFM® blue band connector means they are fast and simple for all staff to replace.
Better Health & Safety
A dramatic reduction in dust in the environment has helped reduce the risk of a combustible dust explosion occurring.
Reduced Downtime
More durable materials and fast, easy changeovers mean downtime is significantly reduced.
What the client said about BFM®
The filling room operators are ecstatic about how their work environment is now dust-free and a “pleasure to work in”.
They no longer spend hours cleaning powder off the surfaces in the filling room or have to regularly remove the messy wire-clamps and socks from the machinery to remove the product build-up between the connectors.
- Production Manager