Case Study: Efficiency Gains For Nutraceutical Processor
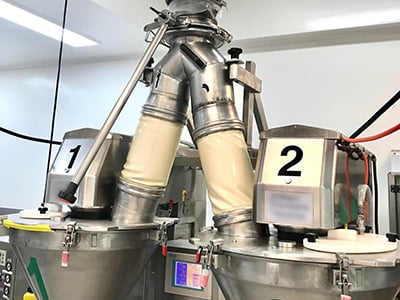
BFM® Provide Impressive Reliability & Efficiency Gains
A leading global manufacturer of science-based nutraceutical products operates their Australian business from a custom-built plant in Queensland where they have a stringent quality-improvement focus and were looking to connect two new machines to be fed from one gravity feed chute.
They tried BFM® fitting for the first time on this particular project in 2009 and made such significant time-savings, they’ve since installed them on all of their powder mixing/transfer bins.
The Challenge
Two machines at the bottom of a single gravity feed needed to be connected in a way that allowed for slight movement of the machines involved as well as constant vibration. They also needed to be fast and easy to remove, clean and replace to avoid any unnecessary production downtime.
Because of the nature of the fine powder being processed and the strict hygiene requirements in the plant, there needed to be a secure seal to ensure there was no product leakage or contamination.
The engineering team also ideally wanted to have visibility of the powder flowing through the connections so they needed to be transparent.
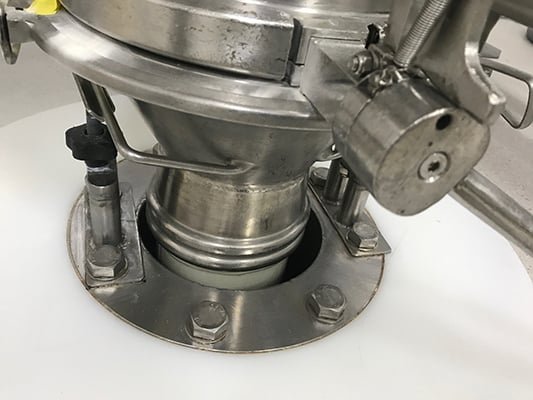
The BFM® Solution
When the two initial BFM® fittings were fitted to the assembly, they immediately halved the usual set-up time for this type of position. The seal of the BFM® connector ensured no product leaked, even with the vibration and slight movement of the machinery.
During cleaning procedures, the connectors were easy to remove and reinstall, and the transparency of the Seeflex connectors also ensured good visibility of product flow through the system.
The BFM® fitting solution really impressed the company who has since installed them in various areas of their powder transfer process and all of their powder mixing/transfer bins now have BFM® fittings on the bottom of them.
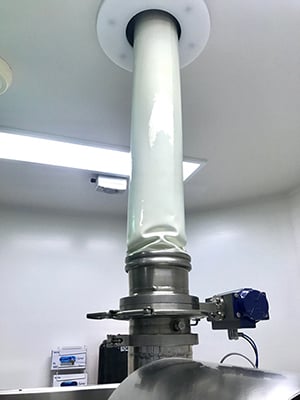
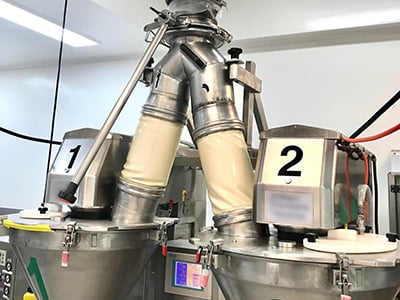
Benefits Achieved
Reduced Downtime
Fast and efficient cleaning in between product runs means downtime has been significantly reduced.
Quick Changeovers
The simple snap-fit of the BFM® makes changeovers and cleaning much faster and easier for operators.
Improved Hygiene
There is zero dust leakage due to the 100% seal and no risk of product contamination, which is imperative in the pharma industry.
Better Health & Safety
No need for tools to remove or install the connector means it's much safer for staff.
Here's what the client said about BFM®:
“Shortly after buying the first two BFM® fittings over 13 years ago, our Continuous Improvement LEAN Process outcomes demanded we purchase more due to the time savings during set-ups, the reliability of a good seal and the ease of assembly and cleaning for our operators. We have never had a BFM® connector let go or lose product which would be a costly event in the pharma industry. We now have them fitted to all our gravity transfer systems and product mixing bins.”
- Engineering Supervisor,
Global Nutraceuticals Manufacturer, (Australia).