Case Study: Hygiene & Safety Gains For Swiss Dairy Company
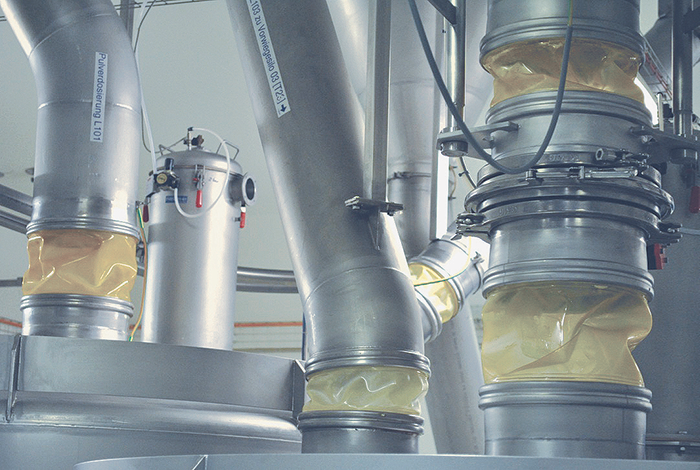
Leakage & Injury Risk Concerns For Infant Formula Processor
HOCHDORF Group is one of the biggest milk processors in Switzerland, processing 300 million kilograms of fresh milk each year. Their Sulgen plant was experiencing issues with the hose clamp connections between processing equipment frequently leaking powder into the factory.
They were also untidy and the hose clips were sharp, causing holes in the connector sleeves themselves and presenting an injury risk to fingers during changeovers.
As part of their continuous improvement process, HOCHDORF turned to BFM® fitting to clean up their processing system and make their changeovers much faster and safer for staff.
The Challenge
There were problems with milk powder leakage and build-up around the clamped connections, as well as issues with the sharp-edged pipe clamps leaving small cracks or holes in the flexible hoses.
The dust leakage was a serious hygiene concern, and the frequent connector changes required due to the damage caused by the hoseclamps (in addition to CIP) meant staff risked injury when manipulating them during replacement.
The time required for this replacement, and constant clean-ups also meant valuable production time was being lost.
Connectors frequently tore, and staff were also spending hours each day cleaning up the powder that leaked continuously from the equipment transitions.
The BFM® Solution
After a successful initial trial, all connectors on one of Hochdorf’s spray-drying tower lines were replaced with the BFM® fitting system.
There were more than 60 different positions requiring replacement and local Distributor Swissfilter worked with the team to ensure all locations were correctly fitted with the best connector for the job.
Now there is no leakage, far less changeovers are required, and when they do need to remove a connector, it is a fast, safe and easy operation. Hochdorf have recently commissioned a brand new spray line with BFM® fittings already installed.
Below shows the variety of locations, sizes and locations BFM® fittings have been installed in at the HOCHDORF plant, which now is clean and dust free.
Benefits Achieved
Better Health & Safety
Because no hose-clips or tools are required, staff now don’t worry about injuring fingers when changing out standard BFM®'s.
Quick Changeovers
Fitting the new BFM® connector is so much easier and faster, with no difficult and sharp hose clips to be manipulated.
Less Downtime
Connector replacement time and CIP processing time has been drastically reduced.
Here's what the client said about BFM®:
"The unique product features of the flexible BFM® connectors have allowed us to achieve perfect production hygiene and a much higher level of employee satisfaction in terms of ease of use and health and safety. I’m definitely a BFM® fan!“
- Production Manager, Baby Care at HOCHDORF Swiss Nutrition AG.
Case study courtesy of BFM® Distributor Swissfilter AG.