Case Study: Cleaner, Safer Factory Achieved With Less Production Downtime
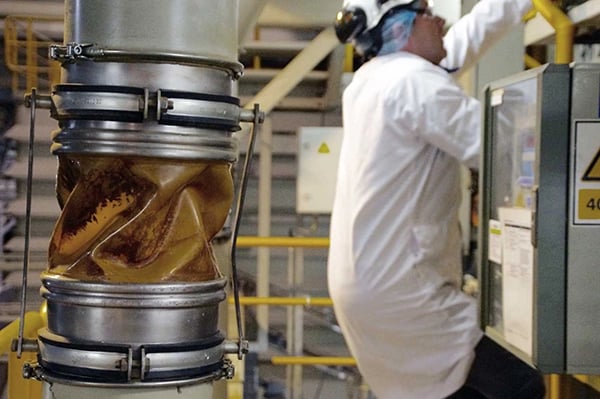
Petfood Hygiene and Efficiency Improvements With BFM®
Spectrum Brands is a global home-essentials manufacturer and is a leading worldwide supplier of petcare products.
The company places high importance on ensuring optimal hygiene and food safety through the use of ‘clean design’ equipment.
Their plant in Coevorden, Netherlands, produces cat and dog food under the brand name Iams, and were concerned about the old-style flexible connectors they were using not being dust tight or durable.
There was also a health and safety risk to staff, particularly during connector replacement, so they were looking for a hygienic, safe solution.
The Challenge
The old-style clamped sleeves that Spectrum Brands were using throughout the plant to feed raw materials into the process were not dust-tight and had a tendency to break easily. This resulted in widespread contamination of the production environment with dust.
To add to this problem, replacing the failed connectors was a complicated and time-consuming process, often requiring installers to use sharp tools and clamps in hard-to-reach areas. This posed a risk to both personnel and production processes.
The downtime and frequency involved was also affecting production efficiency.
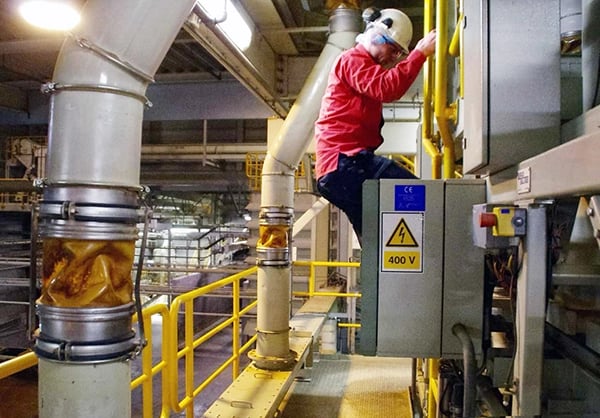
The BFM® Solution
Local Distributor Vlint recommended replacing their old-style clamped sleeves with the BFM® fitting flexible connector system. With Vlint’s advice and expertise, over thirty BFM® fittings were installed in various locations throughout the factory, including under six Rotex sieves.
They provide a dust-tight connection, effectively preventing any pollution in the factory environment. The transparency of the BFM® Seeflex material also provides easy monitoring of product movement through the plant.
The maintenance team is impressed with the durability of the product as they are lasting at least twice as long as the previous connectors. When they do need to be replaced, it’s a fast and easy process with no sharp tools required.
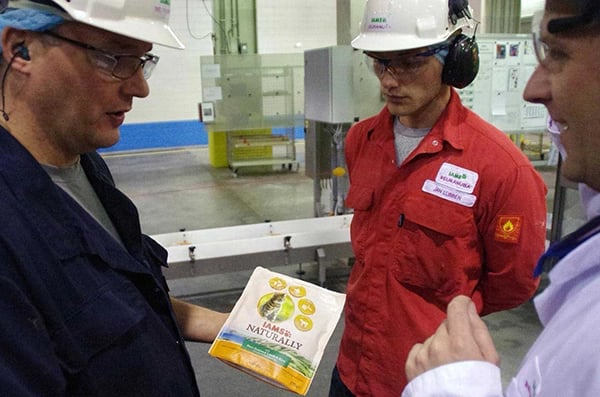
Benefits Achieved
More Hygienic
Dust no longer leaks throughout the plant, meaning a much cleaner factory environment.
Better Health & Safety
There's less risk to installers hands when replacing connectors as no sharp tools are needed for standard connectors.
Reduced Downtime
Staff no longer need to waste time cleaning up leaked product in the screening room and changing out connectors, improving plant efficiency.
What the client said about BFM®:
“In the past, changing a cuff, depending on the location in the factory, took between half an hour and 45 minutes, requiring a lot of work preparation and planning. Now our technicians change the BFM® fittings in just ten minutes.”
- Robert Feringa, Engineer at Spectrum Brands, Coevorden
Case Study courtesy of BFM® Distributor Vlint, Netherlands.